1E: Subsystem Workflow - Detailing the Drivebase
Project Overview
So far, you’ve done the main layout sketches and modeled the frame and bare bellypan.

To finish the drivebase, you will use the content on the following pages to add these details:
-
Battery Mounting: Every robot needs a battery, and while the location may vary based on the other mechanisms present in your robot, it should always be placed as low as possible to make the robot more stable.
-
Electronics Mounting: Adequate space must be allocated on the robot for ease of wiring. Typically, the robot’s electronics are mounted on the bellypan.
-
Bellypan Pocketing: This step is optional. Some teams will prefer to add cutouts in their bellypan to remove weight and make wiring easier. However, pocketing the bellypan may significantly increase machining time.
-
Bumpers and Bumper Mounting: While bumper rules can vary from year to year, they are almost always required to protect your robot and other robots from collisions. Making your bumpers easy to attach and remove is also a very nice quality of life improvement for when you’re at competition.
Note
Even though the first three details won't directly reference the layout sketch, they will reference parts that reference the layout sketch (the frame) and will update accordingly if changes are made.
While the exact implementation for each of these details will vary based on the rest of your robot and from team to team, an example reference for Stage 1E is provided.
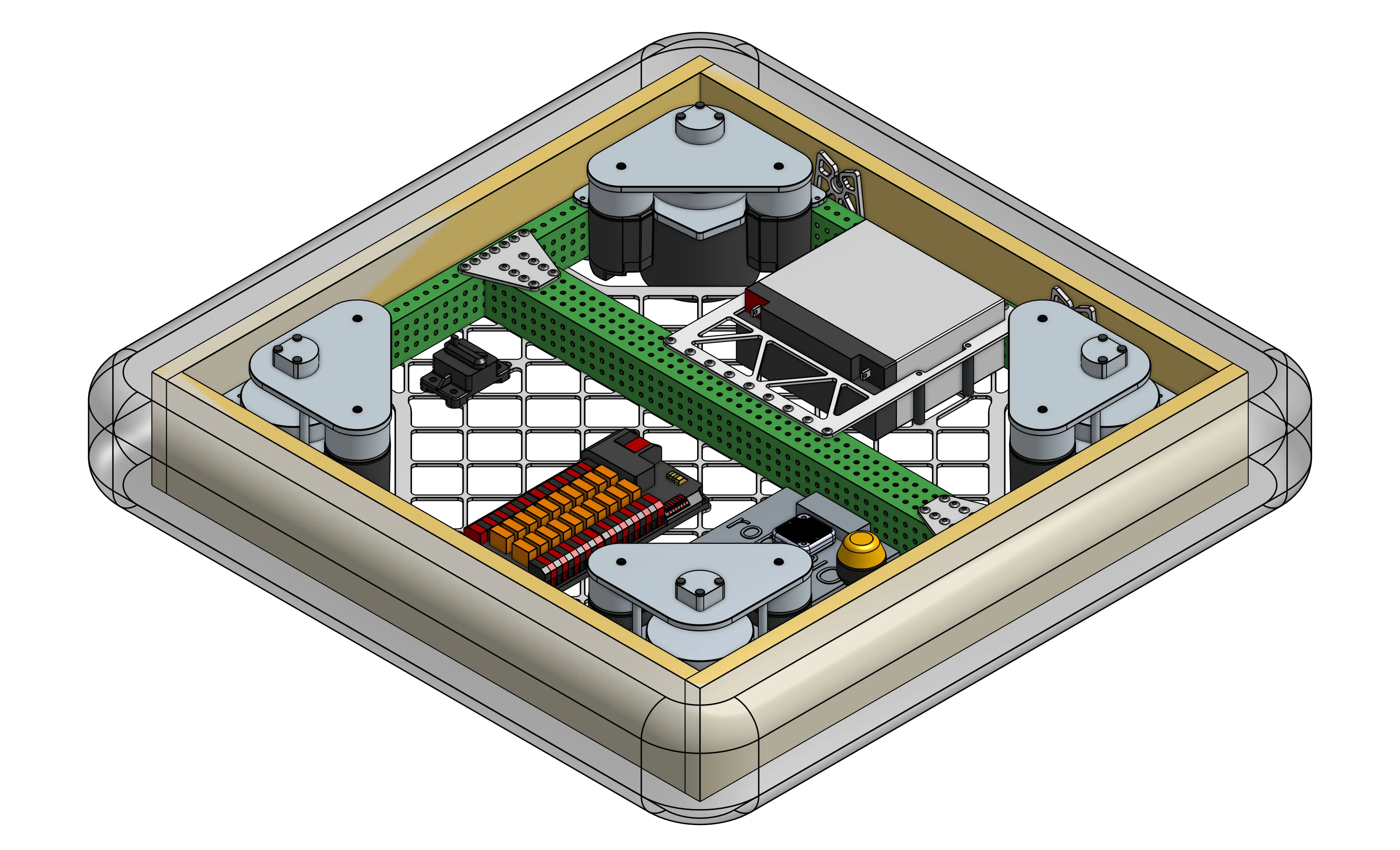
You can access the reference CAD model with the button below. It is based off of the Stage 1D drivebase.
Tip
As you should have a good grasp of part modeling by now, feel free to use your own team's preferences to add details to your drivebase. This can be very open ended.